OVERVIEW
DP-Master manufactures the complete range of Drill Pipes from 2 3/8” OD to 6 5/8” OD in Range 2 and Range 3 sizes up to 46 feet in length. In addition to standard API 5DP specifications, DP-Master also manufactures drill pipe in accordance with the following industry specifications:
- NS-1™
- DS-1
- IRP 1.8 Critical Sour Drilling
- Customer Specifications
- DP-Master Specifications
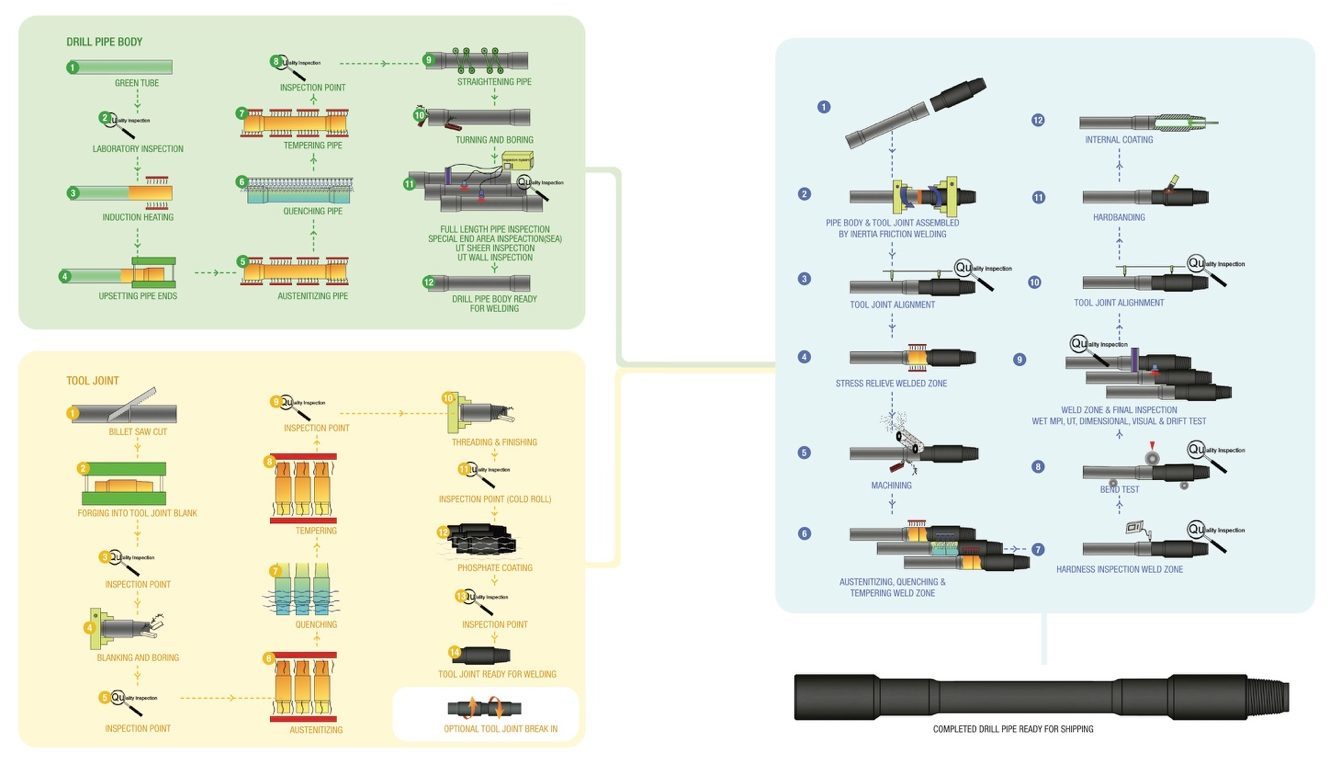
FEATURES AND OPTION
DESIGN
DP-Master incorporates generous internal upset length (miu) and radii to achieve a longer and smoother transition back onto the pipe body ID. This lowers the stress in this very critical section of drill pipe and ensures maximum improvement to the fatigue life of the drill pipe.
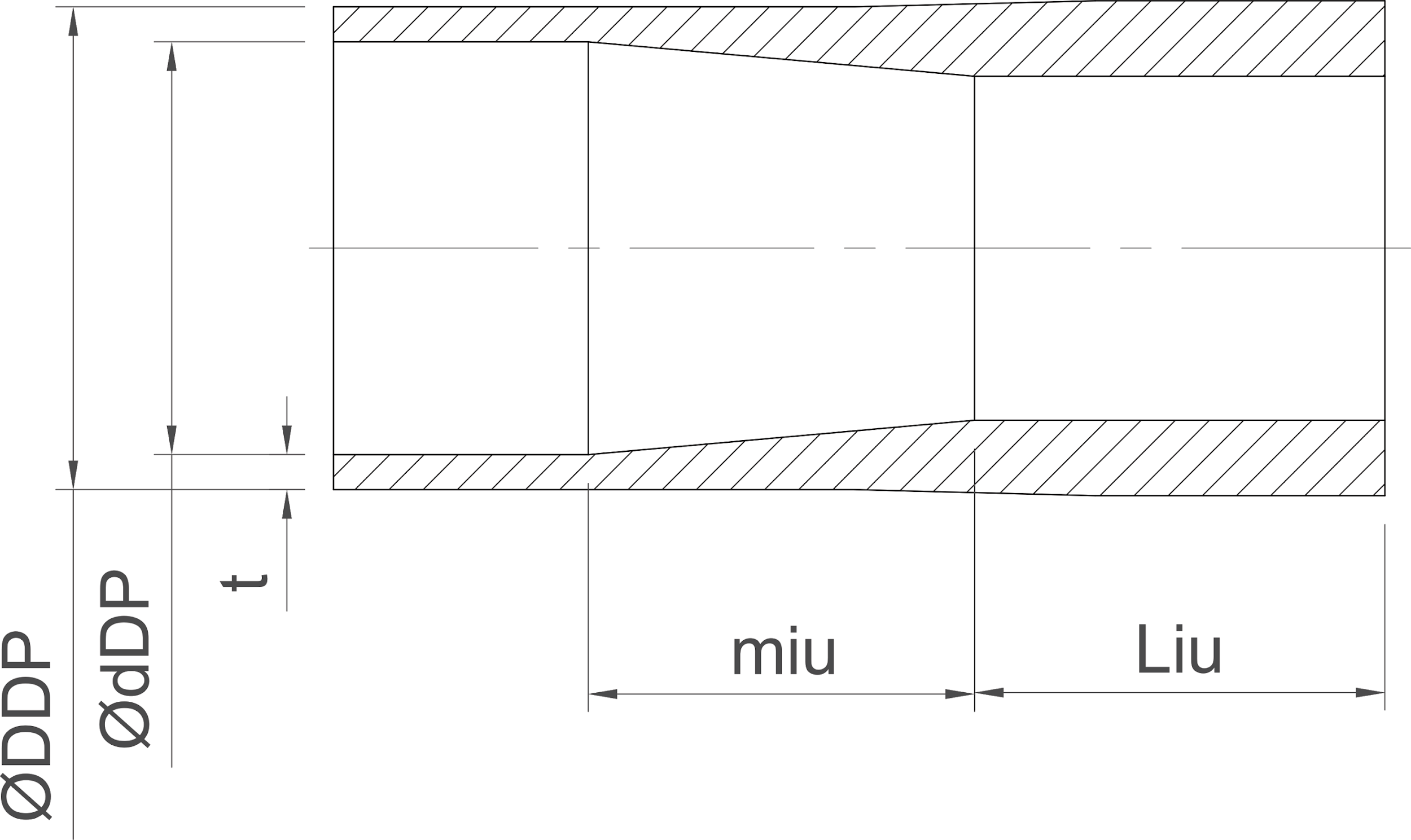
ENHANCED FATIGUE RESISTANCE
Cold rolling of thread roots has demonstrated the beneficial effects to improve fatigue resistance of the connections by minimizing crack initiation.
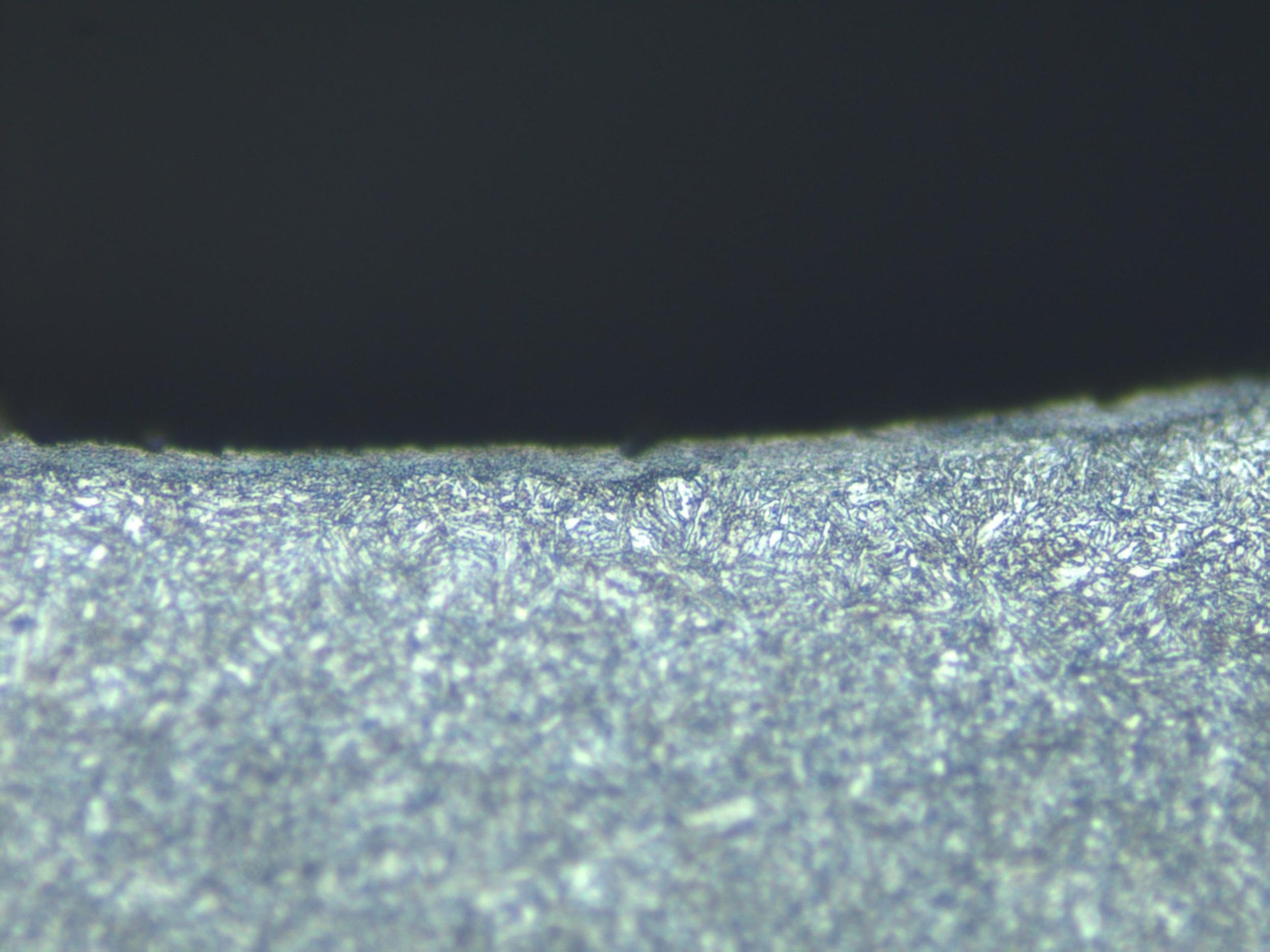
SURFACE PROTECTION
Phosphate coating are applied to tool joints to all threads and seal shoulders of connections to improve anti-galling and corrosion.
TOOL JOINT MAKE & BREAK
Make & break performed under factory controlled procedures helps ensure product consistency. This helps to save valuable rig time and cost while reducing risk of mishandling incident and rig downtime.

HARDBANDING
Hardbanding on the tool joint or wear pad extends the service life of a drill pipe. It can be applied in several configurations to suit clients’ requirements. Hardbanding is applied under closely controlled conditions resulting in a uniform, low porosity, wear resistant surface. DP-Master also delivers smooth hardbanding with machined surface and bevels to reduce casing wear and also to reduce damage to seals in Managed Pressure Drilling (MPD) Rotating Heads.
DP-Master is authorised to apply market proven hardbanding products including ARNCO, Postle, Tuboscope, and Castolin hardbandings.
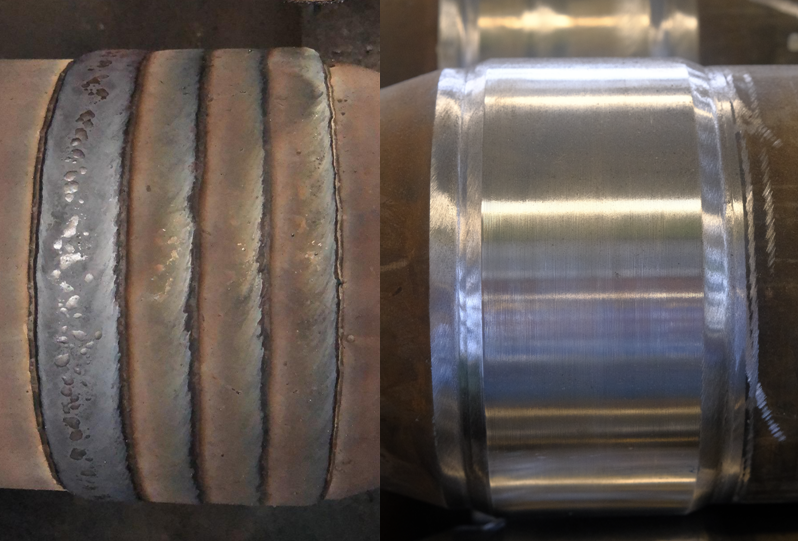
INTERNAL PLASTIC COATING
DP-Master can supply internal plastic coating according to customer requirements. The coating forms a protective layer in the pipe ID to prevent corrosion and thus extend the life span of the pipe in the drilling environment. Internal plastic coating reduces pressure loss inside the drillstring with a 15% improvement in hydraulics.
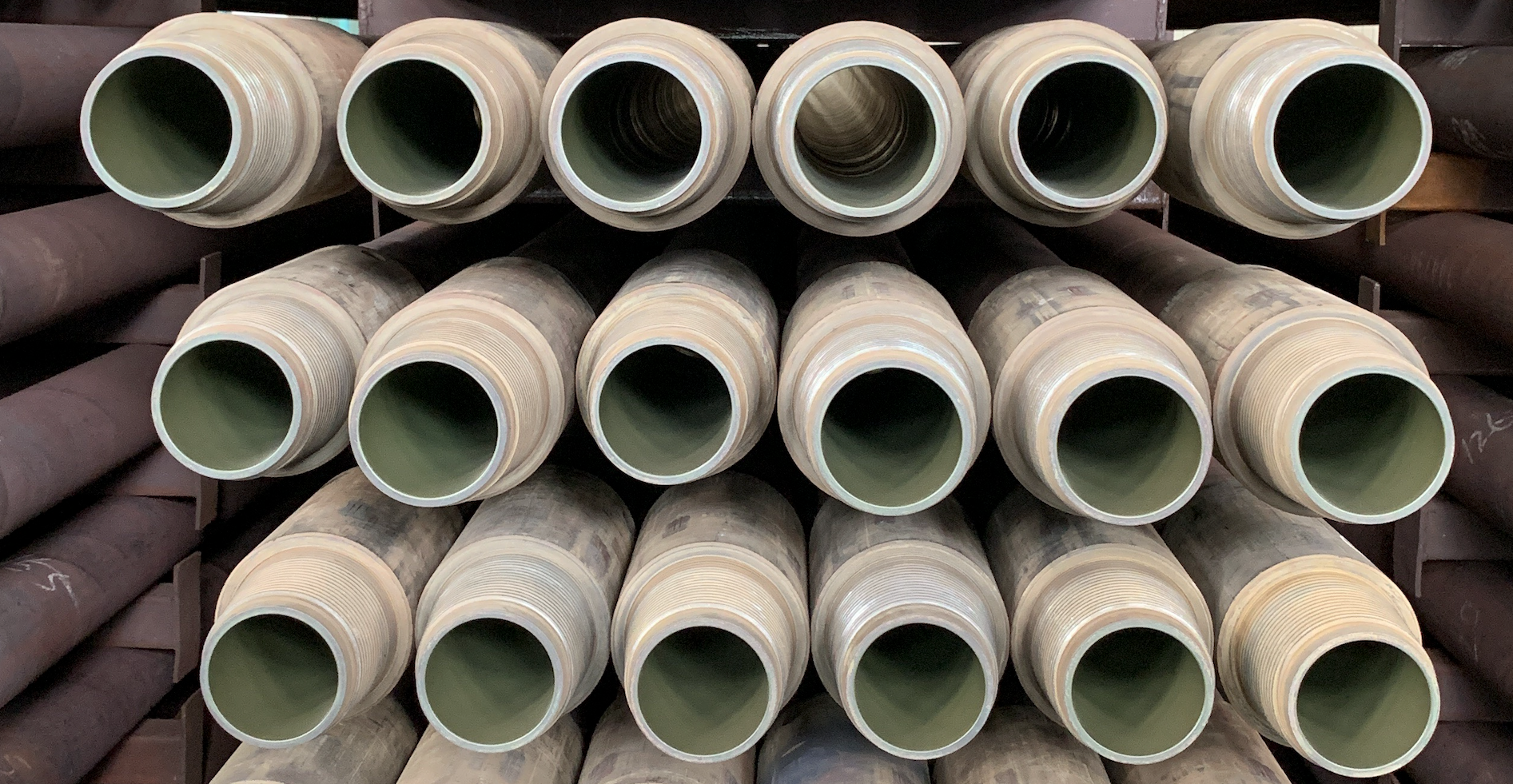
TRACEABILITY AND IDENTIFICATIONS
With an identification system, drill pipe usage can be improved based on better, more accurate data regarding the length of time each pipe has already been use.
DP-Master can perform the installation of brass tags, 2D ID tags, as well as RFID tags on all our products.
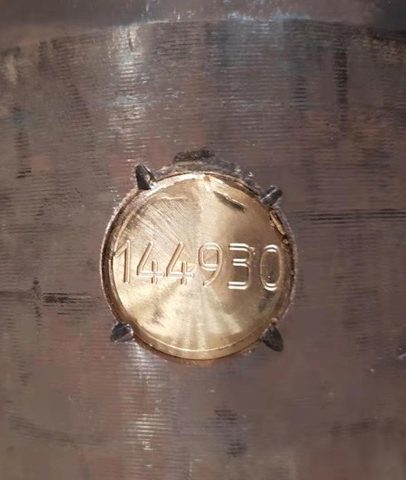
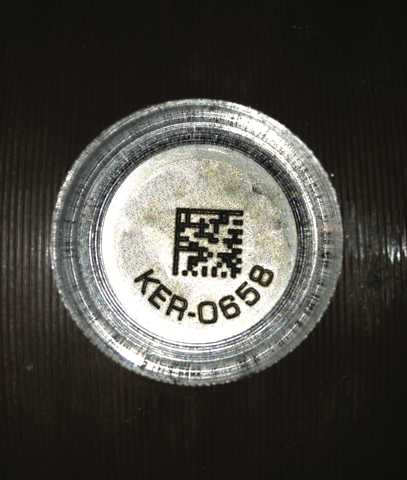
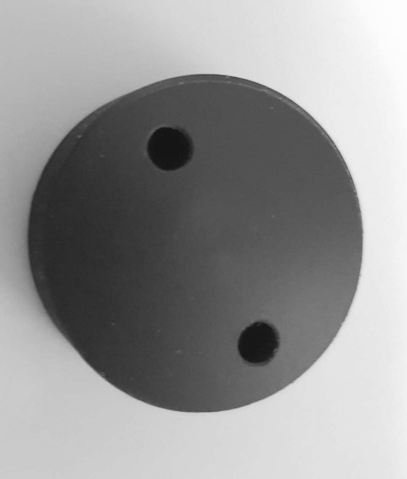
GRADES
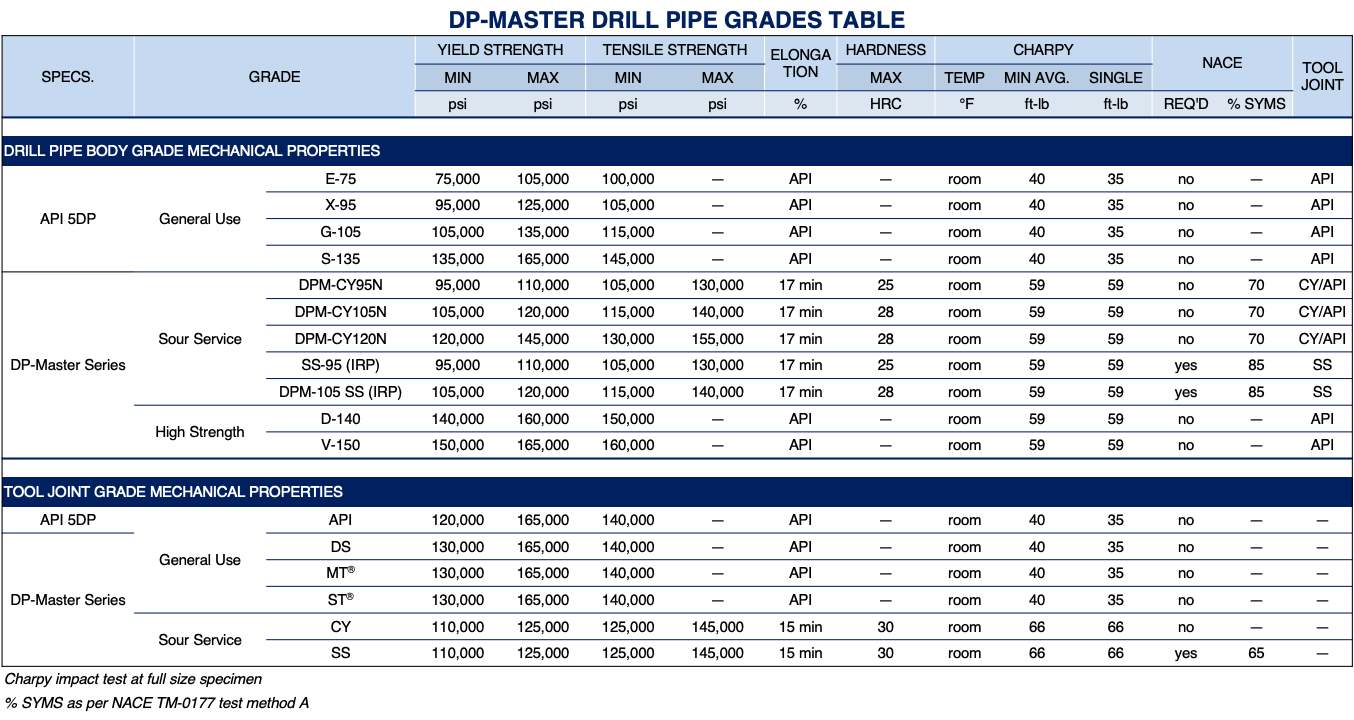
Sour Service Grades
DP-Master’s sour service grade drill pipes are designed for use in H2S environments providing excellent resistance to sulphide stress cracking compared to standard grade drill pipes. Our sour service grades are suitable for a wide range of sour service environments from mild to severe sour environments.
High Strength Grade
With offshore drilling operations being executed in ever-deeper water and extended reach wells, DP-Master’s high strength grades were developed to overcome the demands of the most challenging and complex drilling environments.